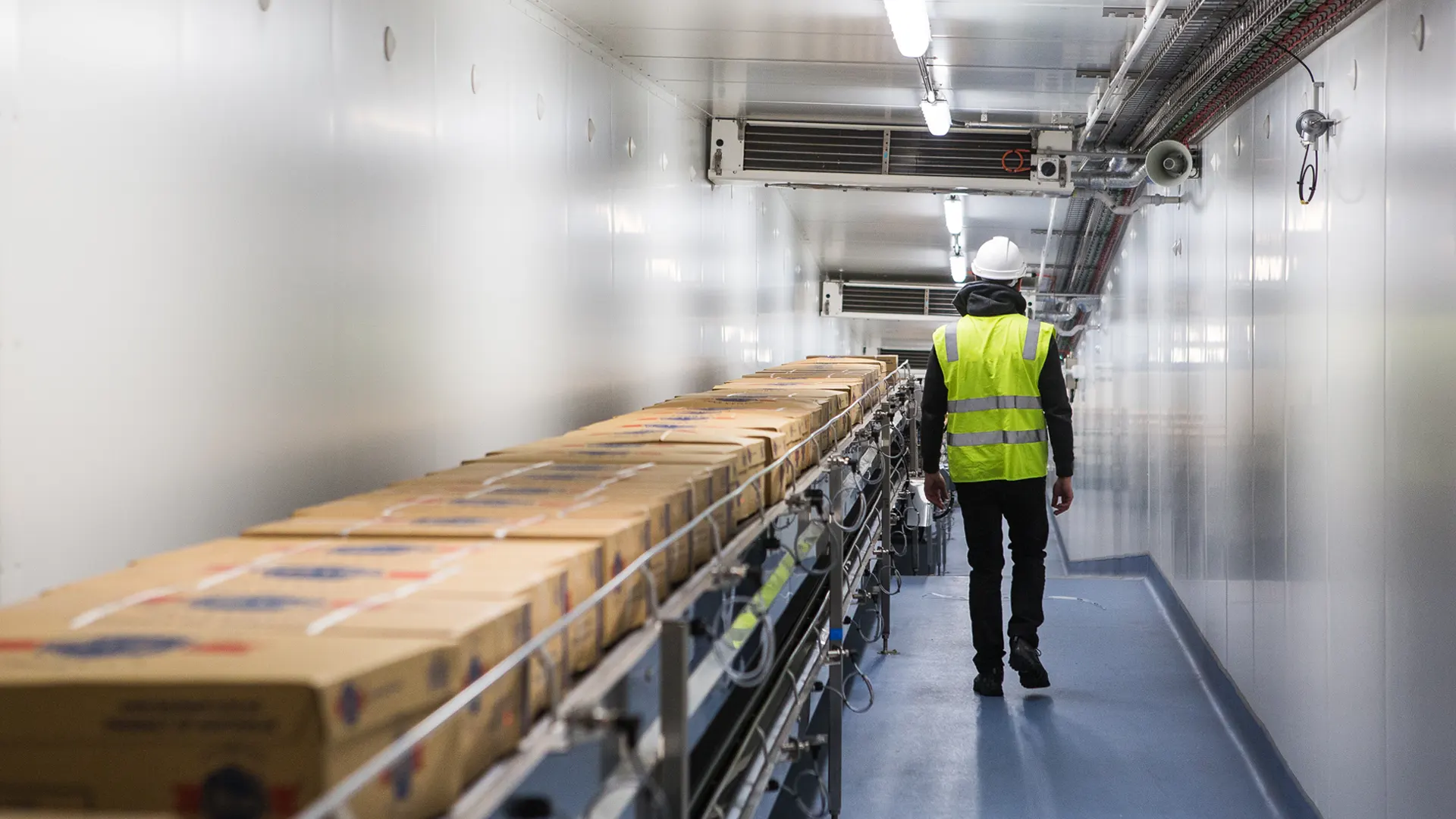
SPARE PARTS & SERVICE
Spare parts and after-sales service are available for all products supplied by MHM Automation.
Spare parts and after-sales service are available for all products supplied by MHM Automation.
MHM Automation's strength is that we deliver what is promised, not just during installation but throughout the entire life of a solution.
Call us today for all your after sales, technical service and spare parts needs.
MHM Automation supports all systems and equipment with a spare part ordering service.
We run a comprehensive tracking system to ensure that the correct parts are allocated for each particular system design.
All components are manufactured to the highest quality and designed to optimise the life, health and efficiency of our systems and equipment.
To place a spare parts order, contact your nearest MHM Automation office.
MHM Automation offers scheduled maintenance programmes to maximise the efficiency and reliability of plant operations.
Our team has the in-depth product knowledge to ensure processes are synchronised for optimum throughput and the prevention of down-time. Reducing wear and tear and improving ease of operation are key areas of focus.
We also provide operator training, including regular refresher sessions, to encourage safe and effective operation of equipment.
Tailored maintenance programmes are developed to meet the needs of each client and their processing operations. These can span maintenance of the complete plant, selected systems within the plant or specific equipment.
Scheduled maintenance programmes include:
We’ve developed a suite of service offerings to help keep your tunnel in top condition and maximise your operating uptime. This includes maintenance, parts, training and support from MHM Automation SRT product experts. Product upgrades and custom control system solutions are also provided.
Flexible options are available including an annual subscription to all of the recommended service inclusions, purchase of individual service packages on an as-required basis or mix-and match selection of components from our service basics range.
Our four distinct service offerings include:
We’ve developed a suite of service offerings to help keep your Milmeq plate freezer in top condition and maximise your operating uptime. This includes maintenance, parts, training and support from our plate freezer product experts. Product upgrades and custom control system solutions are also provided.
Flexible options are available including an annual subscription to all of the recommended service inclusions, purchase of individual service packages on an as-required basis or mix-and match selection of components from our service basics range.
Our four distinct service offerings include:
Remote monitoring is used to provide a constant link with MHM Automation, allowing us to deliver effective on-call support and technical advice anywhere in the world.
Use of a remote monitoring systems enables us to track system performance and identify any issues to take action before a breakdown occurs.
A tailored scheduled maintenance programmes can be delivered to meet operational objectives and ensure ongoing system health.
Remote monitoring can be integrated with the computer-based control system for many of our systems and equipment, with options discussed during the scoping stage of a project.
Our remote monitoring systems typically require:
With more than 60 years’ experience working with food processing operations around the world, MHM Automation has industry experience and a depth of knowledge second to none.
We share this expertise through our assessment and analysis service, which we provide to food processing companies seeking to increase production efficiencies and reduce costs.
This can be delivered as part of initial consultation for customers considering a scheduled maintenance programme or energy management system.
Assessment and analysis of existing process layout and operations is also provided to customers seeking upgrades, extensions or other capital projects.
An assessment of operations identifies opportunities for enhancement; concepts are then developed and costed to achieve the required objectives and suit the operating environment.
Detailed return on investment (ROI) analysis is provided to assist with decision making.
MHM Automation provides an on-call maintenance service. Customers can call us at any stage to report faults or breakdowns.
We will assist with identifying the likely cause and provide support to resolve the issue either remotely or by sending a service provider to site.
Our objectives are to enable operations to be resumed as quickly as possible and to ensure a safe working environment is maintained.
If you require service, please phone your nearest H&C office or sales agent.